INFRARED THERMOGRAPHY
Infrared thermography (IR) is the use of specialized equipment to measure the thermal energy emitted from an object. Thermal energy is light that is not visible because its wavelength is too long to be detected by the human eye. Unlike visible light, in the infrared world, everything with a temperature above absolute zero emits heat.
An infrared camera is a non-contact, non-destructive device that measures thermal energy and converts it to a radiometric image. This image is stored as raw data on the device that is later processed to produce a thermal digital image. During post processing (report preparation) we can precisely measure thermal differences and produce a visual image of our findings. They say a picture is worth a thousand words; infrared thermography is the only diagnostic tool that lets you instantly visualize faults due to thermal patterns.
Nearly everything that uses or transmits power overheats before it fails making thermography a proven cost-effective tool in maintaining the reliability of electrical and mechanical systems.
ELECTRICAL INSPECTIONS
Infrared thermography allows for rapid identification of electrical problems before they fail, saving hundreds if not thousands of dollars in unscheduled repairs. Since electrical components typically give indications of impending failure in the form of increased heat, a proper routine inspection can minimize the potential effects of electrical failures.
As electrical faults develop, the electrical resistance of the offending item (switch, fuse, connections, breaker, etc) will increase, leading to a corresponding increase in temperature until the item finally fails. Heat is often an early symptom of equipment damage or malfunction, making it a key performance parameter monitored in predictive maintenance (PdM) programs. Infrared predictive maintenance regularly checks the temperature of critical equipment, allowing us to track operating conditions over time and quickly identify unusual readings for further inspection. By monitoring equipment performance and scheduling maintenance when needed, our experts help you eliminate the likelihood of unplanned downtime due to equipment failure, spend less on “reactive” maintenance fees and equipment repair costs, extend the lifespan of machine assets, and further maximize maintenance and production. We can detect, document, and provide written reports of electrical components long before they fail.
An annual electrical/mechanical survey will:
-
Accurately pinpoint problems
-
Prevent expensive catastrophic failures
-
Improve efficiency
-
Reduce non-productive downtime
-
Avoid shutdowns and lost revenue
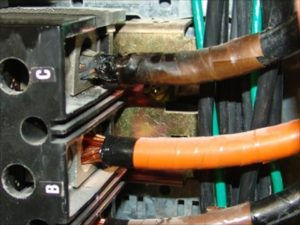
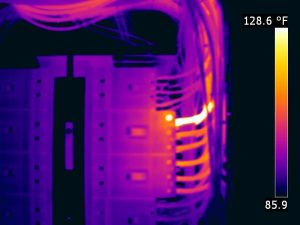
Studies by the Federal Energy Management Program (FEMP) estimate a properly functioning predictive maintenance program can provide a savings of 30% to 40% over reactive maintenance.
Other independent surveys indicate that, on average, starting an industrial predictive maintenance program results in the following savings:
-
Return on investment: 10 times
-
Reduction in maintenance costs: 25% to 30%
-
Elimination of breakdowns: 70% to 75%
-
Reduction in downtime: 35% to 45%
-
Increase in production: 20% to 25%
Infrared thermography cameras are the first line of defense in a predictive maintenance program. Our technicians can quickly measure and compare heat signatures for each piece of equipment on the inspection route without disrupting operations. MEI ELECTRIC has the equipment, knowledge, and training to provide accurate and reliable data in an easy to ready and understandable format.
Give us a call to discuss your infrared electrical survey needs.